

The probes and transducers can be utilized on a "walking stick", on a hand pushed trolley, or in a handheld setup. The techniques mentioned above are utilized in a handful of different ways. EMAT Electromagnetic Acoustic Transducer.Magnetic induction or Magnetic flux leakage - earliest method used to locate unseen flaws in the railway industry.Radiography - used on specific locations (often predetermined) such as bolt holes and where thermite welding was used.
#Fracked oil train car manual#
Magnetic Particle Inspection (MPI) - used for detailed manual inspection.Eddy current inspection - great for surface flaws & near-surface flaws.
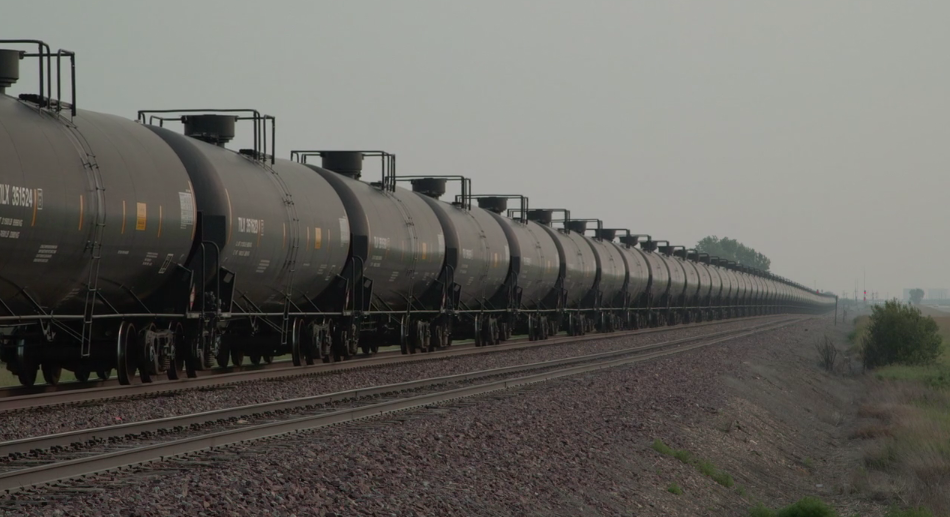
#Fracked oil train car cracked#

#Fracked oil train car crack#
When fluid fills a small crack and a train passes over, the water becomes trapped in the void and can expand the crack tip. One effect that can cause crack propagation is the presence of water and other liquids. Other forms of surface and internal defects: squats - which start as small surface-breaking cracks.These effects include bending and shear stresses, wheel/rail contact stresses, thermal stresses, residual stresses, and dynamic effects.ĭefects due to contact stresses or rolling contact fatigue (RCF): There are many effects that influence rail defects and rail failure. Companies like Sperry Rail Service, Nordco Inc, Herzog Rail Testing, and many others continue to develop an ever-increasing array of technologies to detect internal flaws. Rail inspection continues to advance to this day. Elmer Sperry), by the 1960s Ultrasonic Inspection Systems had been added to the entire Sperry Fleet. In 1949 ultrasonic flaw detection was introduced by Sperry Rail Service (Named after Dr. Since then, many other inspection cars have traversed the rails in search of flaws. This was done by passing large amounts of the magnetic field through the rail and detecting flux leakage with search coils. Magnetic induction was the method used on the first rail inspection cars. Elmer Sperry built a massive rail inspection car under contract with the American Railway Association. With increased rail traffic at higher speeds and with heavier axle loads today, critical crack sizes are shrinking and rail inspection is becoming more important. Further investigation in the late 1920s showed that this type of defect was quite common. The investigation of the accident revealed that the cause was a transverse fissure (a critical crack that lies perpendicular to the length of the rail) in the rail. That particular accident resulted in the death of 29 people and injuries to 60 others. Many sources cite that the need for better rail inspections came after a derailment at Manchester, New York, in 1911. The first rail inspections were done visually and with the Oil and Whiting Method (an early form of Liquid Penetrant Inspection).
